こんにちは!向上 条です。
「なぜなぜ分析って簡単でしょ?」「5回“なぜ?”を繰り返すだけでしょ?」
…そう思っていたけど、実際にやってみると、意外と手が止まってしまう。
- 「そもそも何が原因か分からない…」
- 「なぜ?を5回やっても答えにたどり着かない…」
- 「結局“人のせい”になって終わってしまった…」
こんな経験、ありませんか?
なぜなぜ分析は、シンプルだからこそ奥が深く、「思ったより難しい!」と感じる人がとても多いです。でも、正しく使えば、不良対策・改善活動にとても役立つ“超”実践的なツールなんです!
この記事では、
- なぜなぜ分析の正しいやり方
- 製造現場での具体的な事例
- よくある失敗パターンとその対策
を徹底解説していきます!
QC検定を勉強中の方にも、現場で不良対策を任されて困っている方にも、きっと役立つ内容です!
🔍 なぜなぜ分析とは?基本のやり方とステップ
なぜなぜ分析は、不良やトラブルの「本当の原因(真因)」を探るための原因分析の手法です。
「なぜ?」を繰り返すことで、表面的な問題ではなく、根本にある原因まで掘り下げていきます。
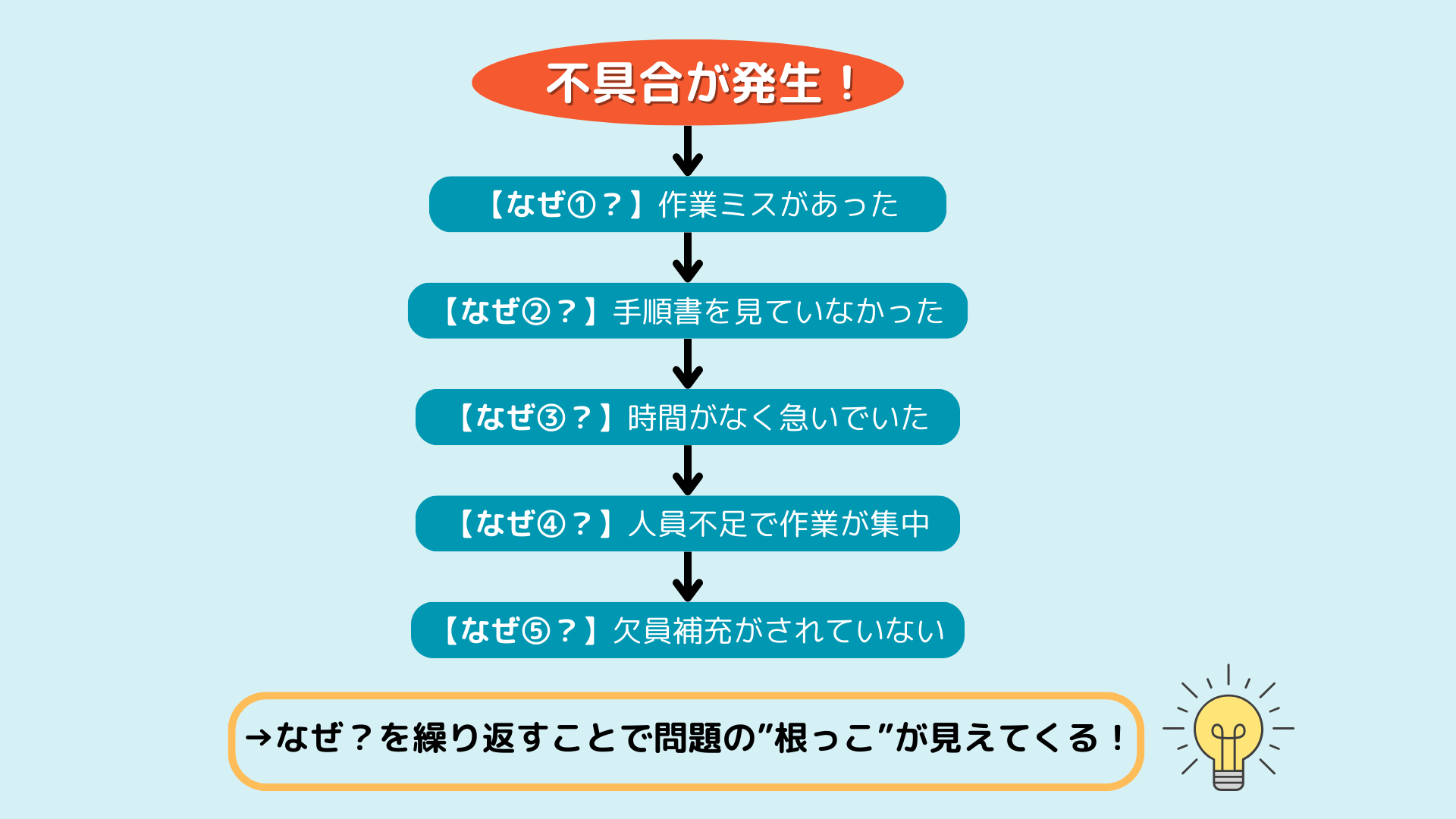
【やり方ステップ|基本の流れ】
- 問題を明確にする(What)
例:「製品にキズがついていた」 - “なぜ?”を繰り返す
・なぜキズがついたのか?
・なぜその作業でキズがついたのか?
・なぜその作業をしていたのか?
…という具合に、本質に迫るまで掘り下げます - 真因にたどり着いたら、対策を考える
対策は「確認を強化する」「注意喚起をする」などの曖昧なものではなく、仕組みやルールの改善に落とし込むのがポイント!
❓ 「なぜ」は何回繰り返すの?
一般的には「5回繰り返す」と言われますが、回数にこだわる必要はありません!
- 3回で真因が見えることもある
- 6回以上かかることもある
📌 大事なのは「深さ」より「納得感」!
「これ以上掘っても意味がない」と感じる“納得できる理由”にたどり着くことがゴールです。
📚 具体事例で学ぶ!なぜなぜ分析の使い方
「なぜなぜ分析って実際どう使うの?」という方のために、製造現場でよくある3つの事例をご紹介します!
✅ 事例1|製造パターン:キズ不良の原因を分析
問題:製品の側面にキズがついていた
なぜ?① 搬送装置のレールにぶつかっていた
なぜ?② レールの固定が緩んで位置がずれていた
なぜ?③ 固定用のボルトがゆるんでいた
なぜ?④ 定期点検でレールの位置確認をしていなかった
なぜ?⑤ 点検項目に「レール位置」が含まれていなかった
なぜ?⑥ 点検項目が5年以上更新されておらず、現場の変化が反映されていなかった
✅ 真因:点検項目の更新がされておらず、必要なチェックが漏れていた
🎯 対策:点検表を最新化し、レールの位置チェックを追加。更新ルールも明文化する。
✅ 事例2|検査パターン:寸法不良が多発
問題:検査で寸法外れが多発している
なぜ?① 測定器の値がズレていた
なぜ?② ゼロ点調整がされていなかった
なぜ?③ 新人が調整方法を知らなかった
なぜ?④ 測定器の取扱マニュアルが整備されていなかった
✅ 真因:測定器の使い方がマニュアル化されておらず、新人教育も不十分だった
🎯 対策:使用手順書を作成し、新人教育に組み込む。定期的な教育も実施。
✅ 事例3|ヒューマンエラー:作業ミスの再発
問題:製品に部品の入れ忘れがあった
なぜ?① 作業者が部品を入れ忘れた
なぜ?② 作業工程にチェックリストがなかった
なぜ?③ 作業の簡略化が優先されていた
なぜ?④ 過去のミスが少なく、改善提案も少なかった
なぜ?⑤ 定期的な作業見直しや再教育の文化が根付いていなかった
✅ 真因:作業改善の仕組みがなく、ミスが見過ごされていた
🎯 対策:チェックリスト導入とあわせて、改善提案制度を整備。現場主導の仕組み見直しを促進。
⚠️ よくある失敗と落とし穴
なぜなぜ分析はとても便利なツールですが、やり方を間違えると逆効果になることも!
ここでは、よくある失敗パターンとその背景を紹介します。
❌ ①「なぜ?」がすべて“人のせい”になる
例:
・「なぜ?→作業者がミスした」
・「なぜ?→注意が足りなかった」
このように、すぐに“ヒューマンエラー”で片付けてしまうと、改善にはつながりません!
重要なのは、「なぜそのミスが起きたのか?」という 背景の仕組みや環境に目を向けることです。
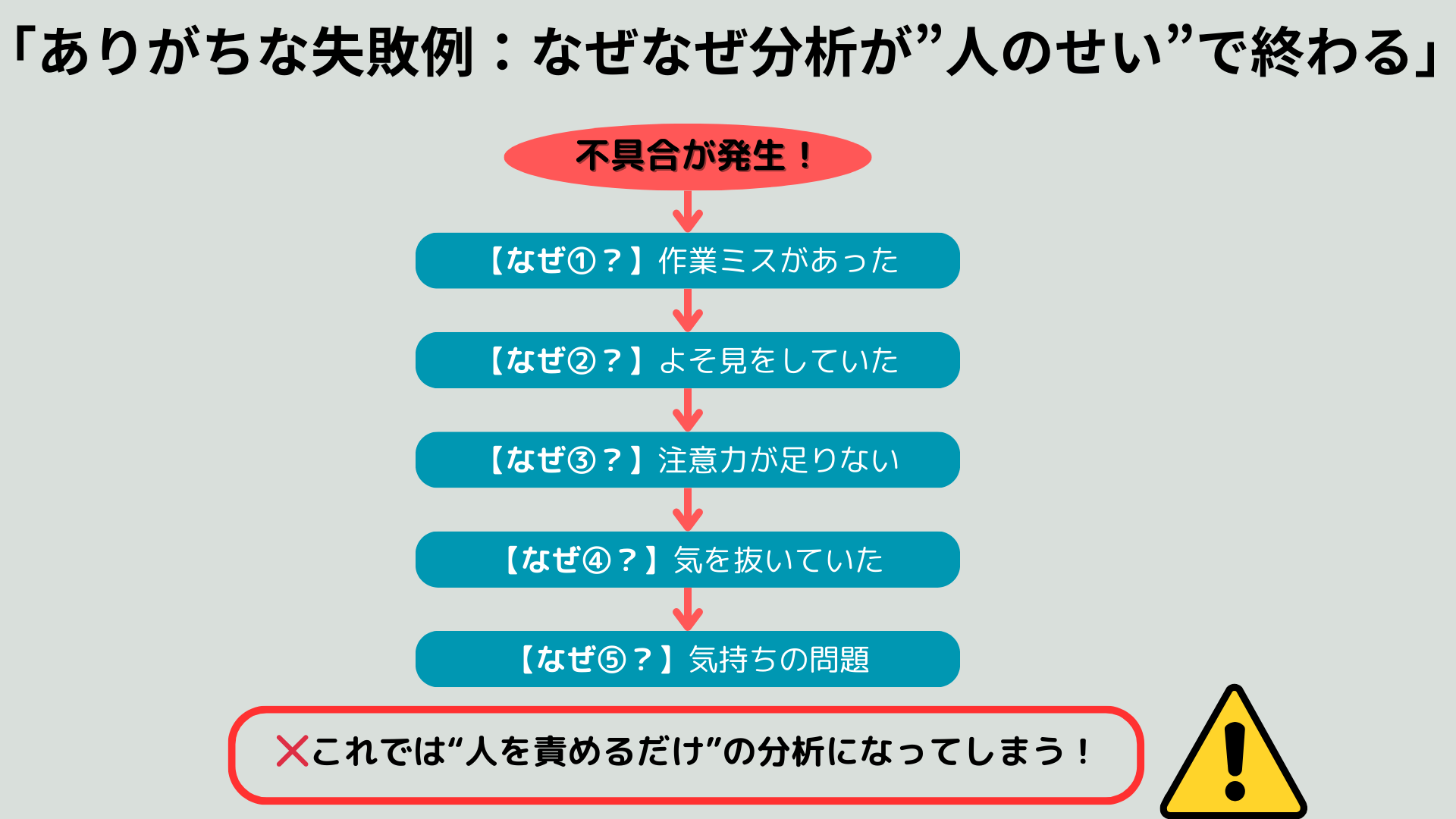
❌ ② 「確認する」「気をつける」が対策になってしまう
例:
・「次回から気をつけます」
・「ダブルチェックします」
📌 これは対策ではなく“願望”です。
人は忘れるし、ミスもします。人任せの運用では再発防止になりません。
🔍 「どうすれば再発しないか?」という仕組みの工夫が必要です。
❌ ③ 推測だけで進めてしまう
現場に行かず、データも見ず、「たぶんこうだろう」で進めるのは危険!
事実を元にしない分析は、ズレた対策になる可能性大です。
✅ 5W1H(いつ・どこで・誰が・何を・なぜ・どのように)を意識して、事実を正確に把握しましょう!
❌ ④ なぜが深掘りできていない(2~3回で終わってしまう)
「なぜ?」を繰り返しても、根本にたどり着く前に止まってしまうことがあります。
背景には…
- 組織の都合で深掘りしづらい
- 忙しくて時間が取れない
- 真因が見えにくい
📌 「それって本当の原因?」と自問自答することが、深掘りのカギになります!
❌ ⑤ 原因が“曖昧な言葉”になっている
例:
・「慣れていなかった」
・「理解が浅かった」
・「注意不足だった」
これでは対策が立てられません!
✅ 行動・仕組み・環境など、“変えられること”に落とし込むことがポイントです。
✨ なぜなぜ分析をうまく進めるコツ
「なぜなぜ分析ってなんか難しい…」と思っていませんか?
でも実は、ちょっとしたコツを意識するだけで、グッと効果的に進めることができるんです!
✅ ① チームでやる!一人で抱え込まない
一人で考えると、視点が偏りがち。
複数人でやることで多角的に原因を掘り下げることができます。
特に現場の人・検査の人・設計の人など、違う立場の人がいるとベスト!
「現場ではそう見えてるのか!」という気づきもたくさん生まれます。
✅ ② 責任追及ではなく、“再発防止”が目的
分析の目的は「誰が悪いか?」を探すことではありません!
もしも責任追及の空気になると…
- 原因を隠そうとする
- 本音が出なくなる
- 表面的な対策になる
みんなが安心して意見を出せる雰囲気づくりが大切です!
✅ ③ 再発を防げる“仕組み”を考える
「気をつける」や「確認する」だけでは再発防止はできません!
仕組みに落とし込んでこそ、なぜなぜ分析は活きてきます。
例:
- チェックシートに項目を追加する
- 作業標準書をわかりやすく更新する
- ポカヨケ(ミス防止の仕組み)を導入する
“人が頑張らなくてもミスが起きない状態”を目指しましょう。
✅ ④ 属人化をなくす
「○○さんしか分からない」はとても危険!
その人が休んだ・辞めた…その時に重大な品質問題に発展することも。
なぜなぜ分析で見つけた改善ポイントは、ルール化・標準化して誰でもできるように!
✅ ⑤ 継続して振り返る
1回分析して終わりではなく、その後の効果確認も大切。
- 対策はちゃんと定着しているか?
- 再発は起きていないか?
- もっと良くできないか?
分析→対策→確認→再分析…と、PDCAを回すことが品質向上につながります!
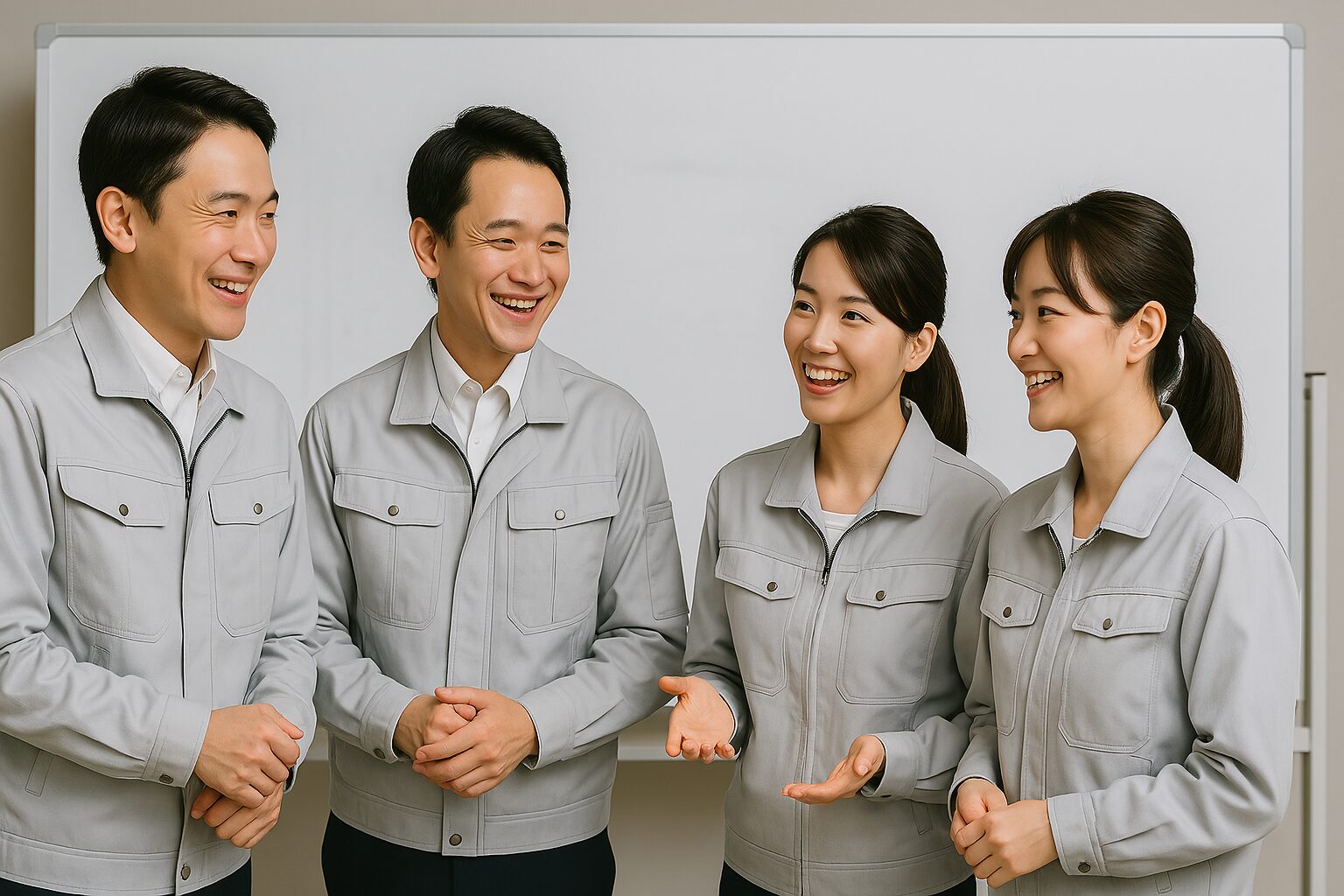
関連記事
せっかく原因を分析しても、“形だけのルール”では意味がありませんよね。
こちらの記事では、実際に“使われる仕組み”をどう作るか?を詳しく紹介しています。
👉 🧠守られないルールの原因と改善方法|現場に合った仕組みの作り方
🧭 品質改善をもっと深く学びたい方へおすすめの記事
✅ まとめ|なぜなぜ分析を仕事に活かす
「なぜなぜ分析」はうまく書くことが目的ではありません。
大事なのは、“気づき”と“次に活かすこと”。完璧じゃなくても、意味のある一歩になります。
🔹 今回の記事で伝えたこと
✅ なぜなぜ分析は、「原因」を深掘りし「仕組み」で防ぐための手法
✅ 5回にこだわらず、納得できるまで掘り下げるのがコツ
✅ 1人で考えず、チームで取り組もう
✅ 責任追及ではなく、“再発防止”が目的
✅ 対策は「気をつける」ではなく「仕組み」に!
🌱 少しずつ、でも確実に前進を
最初は難しく感じても大丈夫です。
「なんで?」と問い続ける力は、**どんな仕事にも応用がきく“思考の筋トレ”**になります。
「また同じミスが起きた…」
「改善したはずなのに再発してしまった…」
そんな時こそ、なぜなぜ分析の出番です。
💬 この記事を読んだあなたへ
「今までよく分からなかったけど、ちょっとやってみようかな」
そう思ってもらえたなら、この記事の目的は大成功です!
ぜひ、実際の現場で1つでも使ってみてください!
小さな改善が、あなたの現場を確実に前に進めてくれます!
📌 関連リンク
👉 QC検定3級の勉強法まとめ!初心者でも合格できるコツ【2025年最新】
👉 品質管理とは?QC検定3級にも役立つ!初心者がつまずきやすい落とし穴と改善の考え方
👉 改善したいけど時間がない人へ|忙しい現場が変わる最初の一歩と考え方
コメント